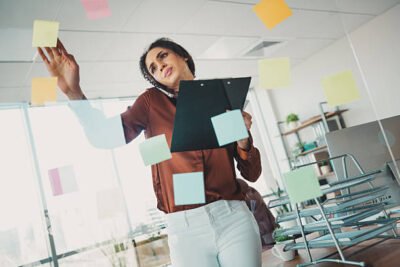
Manutenção Industrial: A Chave para a Eficiência
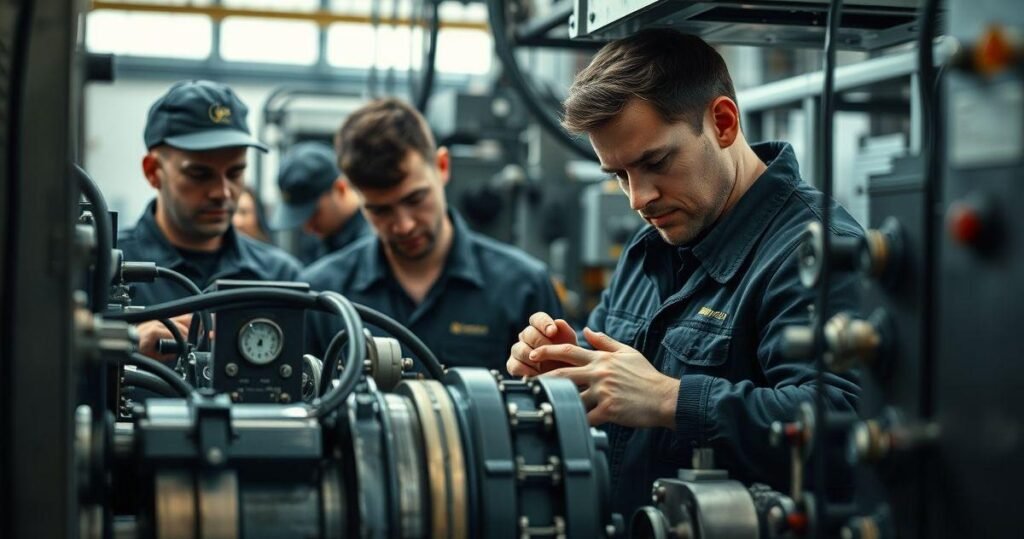
Em um cenário industrial cada vez mais competitivo e automatizado, a manutenção deixou de ser apenas uma medida corretiva para assumir um papel estratégico dentro das organizações.
Mais do que consertar falhas, a manutenção industrial moderna busca antecipar problemas, garantir a continuidade dos processos produtivos e preservar o desempenho dos equipamentos.
É por isso que, hoje, pensar em manutenção é pensar em desempenho, segurança e sustentabilidade.
- O Papel Estratégico da Manutenção Eletromecânica nas Indústrias Modernas
- Como Implementar Um Plano de Manutenção Preventiva
- Os Benefícios da Manutenção Preditiva na Indústria
- Erros Comuns na Manutenção de Equipamentos Eletromecânicos
- A Importância do Treinamento da Equipe de Manutenção
- Garantindo a Performance Industrial através de Uma Manutenção Eficiente.
O Papel Estratégico da Manutenção Eletromecânica nas Indústrias Modernas
A manutenção eletromecânica desempenha um papel crucial na operação eficiente de equipamentos e maquinários em indústrias de todos os setores.
Essa prática envolve a combinação de técnicas eletroeletrônicas e mecânicas para garantir que os sistemas funcionem sem interrupções, aumentando a produtividade e reduzindo custos operacionais.
Com o avanço tecnológico, a necessidade de uma manutenção preventiva e preditiva se torna indispensável para evitar falhas inesperadas.
Um dos principais métodos utilizados na manutenção eletromecânica é a manutenção preditiva, que se baseia em monitoramento contínuo e análise de dados.
Dessa forma, é possível identificar sinais de desgaste e tomar medidas antes que uma falha ocorra, o que economiza tempo e recursos.
Muitas empresas estão adotando essa abordagem, utilizando sensores e sistemas de monitoramento remoto para garantir que seus maquinários estejam sempre em condições ideais.
A manutenção corretiva, que se refere à reparação de equipamentos após uma falha, ainda é uma prática comum.
Entretanto, este método pode resultar em paradas inesperadas, afetando negativamente a produtividade.
Por isso, o investimento em equipamentos de manutenção e em treinamento de mão de obra qualificada se torna crucial.
Profissionais capacitados são capazes de diagnosticar problemas rapidamente e implementar soluções eficazes.
A eficiência energética também está diretamente ligada à manutenção eletromecânica.
Equipamentos bem mantidos operam com menor consumo de energia, contribuindo para a sustentabilidade e redução de custos.
A automação industrial está se tornando cada vez mais comum no processo de manutenção eletromecânica.
Sistemas automáticos podem realizar diagnósticos e, às vezes, realizar reparos simples sem intervenção humana.
As empresas que investem em automação frequentemente notam um aumento significativo na eficiência operacional e na qualidade dos produtos.
O gerenciamento adequado dos processos de manutenção pode, de fato, ser a chave para uma operação industrial bem-sucedida.
Ao implementar sistemas e estratégias eficientes, como o uso de software de gestão de manutenção (CMMS), as indústrias conseguem otimizar seus recursos e maximizar a produção.
Essas plataformas permitem que as empresas planejem manutenções, rastreiem custos e analisem dados históricos para melhorar continuamente suas operações.
As indústrias que ignoram a manutenção eletromecânica correm o risco de enfrentar falhas graves, interrupções de produção e, consequentemente, perda de competitividade no mercado.
Portanto, é vital desenvolver uma cultura de manutenção entre todos os colaboradores, assegurando que a manutenção não seja somente uma responsabilidade do setor técnico, mas sim uma prioridade para toda a organização.
Como Implementar Um Plano de Manutenção Preventiva
A implementação de um plano de manutenção preventiva é essencial para garantir a eficiência e a durabilidade dos equipamentos industriais.
Um plano bem estruturado pode prevenir paralisações inesperadas, reduzir custos operacionais e melhorar a segurança do ambiente de trabalho.
Para começar, é crucial realizar um levantamento detalhado dos ativos que precisam de manutenção.
Essa lista deve incluir informações como data de aquisição, histórico de manutenções anteriores, e frequência de uso.
Uma vez que a lista de equipamentos esteja pronta, o próximo passo é definir a periodicidade das manutenções.
Isso pode variar conforme o tipo de equipamento e seu regime de operação.
Para ajudar nesse processo, muitos profissionais recorrem a normas técnicas e referência do setor.
A criação de um cronograma de manutenção que indique os prazos e tipos de serviço é vital. Essa ferramenta deve ser clara e acessível a todos os envolvidos.
É fundamental capacitar a equipe que irá executar os procedimentos de manutenção.
Oferecer treinamentos periódicos, workshops e orientações sobre as melhores práticas pode aumentar a eficiência e a qualidade do serviço prestado.
A manutenção deve ser realizada por profissionais qualificados, que compreendam a importância de seguir as rotinas estabelecidas.
A comunicação aberta entre os operadores e a equipe de manutenção é também um ponto-chave para o sucesso do plano.
Ao longo da execução do plano, é imprescindível monitorar e registrar todas as ações realizadas.
Isso inclui anotar detalhes como peças trocadas, tempo gasto em cada atividade e quaisquer anomalias encontradas.
Esses dados ajudam a manter um histórico confiável e podem ser úteis para futuras análises e melhorias nos processos de manutenção.
A implementação de técnicas de manutenção eletromecânica industrial pode trazer ainda mais eficiência e confiabilidade ao sistema.
É importante revisar o plano de manutenção preventiva de forma regular.
Com o passar do tempo, novas tecnologias e métodos podem surgir, e o que era eficaz anteriormente pode precisar de ajustes.
Feedback da equipe e análise dos resultados obtidos devem ser considerados durante essas revisões, garantindo que o plano se mantenha sempre alinhado com as necessidades reais da operação.
Os Benefícios da Manutenção Preditiva na Indústria
A manutenção preditiva é uma estratégia moderna que se destaca na melhoria do desempenho operacional das indústrias.
Ela utiliza técnicas de monitoramento e análise de dados para prever falhas em equipamentos antes que ocorram, permitindo intervenções mais eficientes.
Uma das principais vantagens da manutenção preditiva é a otimização dos recursos financeiros.
Empresas que a adotam frequentemente observam uma redução significativa nos gastos relacionados a manutenções emergenciais.
Além das economias financeiras, a manutenção preditiva promove um ambiente de trabalho mais seguro.
Ao monitorar constantemente o funcionamento das máquinas, é possível identificar e mitigar riscos que poderiam levar a acidentes.
Isso protege os colaboradores e preserva o patrimônio da empresa, pois menos falhas significam uma menor probabilidade de danos a equipamentos caros.
- Melhoria na eficiência operacional;
- Aumento da confiabilidade;
- Planejamento estratégico;
- Integração da tecnologia.
Outro ponto importante a ser destacado é a integração da tecnologia.
Ferramentas como sensores IoT e análise de big data são fundamentais na manutenção preditiva.
Esses recursos possibilitam um acompanhamento em tempo real do estado dos equipamentos, facilitando a detecção de vibrações anômalas ou alterações de temperatura.
Este tipo de tecnologia pode ser especialmente vantajoso em setores que dependem de compressores, como mencionado na manutenção em compressor de ar.
Erros Comuns na Manutenção de Equipamentos Eletromecânicos
A manutenção de equipamentos eletromecânicos é fundamental para garantir a eficiência e a longevidade dos sistemas industriais.
Entretanto, alguns erros são recorrentes e podem comprometer esse objetivo. Um dos principais erros é a falta de um cronograma de manutenção.
Sem um planejamento adequado, é fácil negligenciar verificações importantes, o que pode levar a falhas inesperadas e custos elevados.
Outro erro comum é a utilização de peças de reposição inadequadas.
Substituir componentes por versões não originais ou de qualidade inferior pode resultar em desempenho insatisfatório e danos ao equipamento ao longo do tempo.
É vital sempre optar por peças recomendadas pelos fabricantes, assegurando que todos os padrões de qualidade sejam respeitados.
A falta de treinamento adequado para os operadores e a equipe de manutenção pode gerar sérios problemas.
Sem o conhecimento necessário, esses profissionais podem não identificar falhas em potencial ou realizar manutenções incorretas.
Investir em capacitação e treinamentos regulares é essencial para maximizar a eficiência operacional.
A manutenção preventiva é frequentemente subestimada.
Quando se espera que o equipamento quebre para realizar reparos, os custos podem ser exorbitantes.
A implementação de uma abordagem preventiva pode ajudar a detectar problemas antes que se tornem críticos, evitando interrupções na produção.
Igualmente importante é a atenção às especificações de instalação.
Equipamentos mal instalados podem apresentar falhas operacionais desde o início.
Portanto, é crucial seguir os manuais do fabricante e garantir que os técnicos estejam cientes das melhores práticas.
Um erro muitas vezes ignorado é a falta de documentação da manutenção realizada.
A manutenção deve ser registrada de forma detalhada, o que permite monitorar o histórico do equipamento e facilitar futuras intervenções.
Essa prática é especialmente importante para a manutenção em redutores, onde a continuidade do acompanhamento pode fazer toda a diferença na performance e durabilidade do equipamento.
A Importância do Treinamento da Equipe de Manutenção
O treinamento da equipe de manutenção é um fator crucial na operação eficiente de qualquer empresa que utiliza maquinário pesado, como empilhadeiras.
Um time bem treinado garante a continuidade das operações e minimiza riscos, reduz custos e aumenta a vida útil dos equipamentos.
Equipamentos mal mantidos podem resultar em paradas inesperadas e dispendiosas, além de aumentarem os riscos de acidentes e danos.
Com uma formação adequada, os profissionais de manutenção ficam mais preparados para realizar diagnósticos precisos e executar reparos.
A manutenção preventiva é uma prática que se beneficia diretamente do conhecimento adquirido em treinamentos.
Quando a equipe é capacitada para identificar sinais de desgaste e problemas potenciais, é possível evitar falhas mais sérias.
Em indústrias que operam com manutenção empilhadeira elétrica, por exemplo, é fundamental que os técnicos conheçam a fundo o funcionamento dos motores elétricos e seus sistemas de controle, garantindo intervenções eficazes e seguras.
Além das competências técnicas, o treinamento também pode abordar questões de segurança e regulamentação.
Profissionais que conhecem as normas de segurança do trabalho e as práticas recomendadas estão mais aptos a prevenir acidentes.
Uma equipe bem treinada se torna mais eficiente e promove um ambiente de trabalho mais seguro, o que é fundamental para a satisfação e retenção de funcionários.
A atualização constante da equipe de manutenção é essencial, dado que as tecnologias e procedimentos estão em evolução.
Treinamentos periódicos garantem que todos estejam alinhados com as melhores práticas do mercado, levando a uma performance superior e maior inovação nas abordagens de manutenção.
Garantindo a Performance Industrial através de Uma Manutenção Eficiente.
A manutenção industrial eficiente é um pilar fundamental para garantir a performance e a competitividade das empresas no mercado atual.
Principais práticas de manutenção incluem:
- Manutenção preventiva: a realização de inspeções regulares e substituições programadas que evitam falhas inesperadas.
- Manutenção preditiva: utilização de tecnologias para monitorar a condição dos equipamentos e prever quando a manutenção é necessária.
- Manutenção corretiva: resposta rápida a falhas quando estas já ocorrem, minimizando o tempo de paralisação.
Um plano de manutenção bem estruturado pode ser definido através da análise de dados históricos de falhas e desempenho dos equipamentos.
Esse planejamento deve considerar a criticidade de cada máquina e sua contribuição para a linha de produção, garantindo que as operações essenciais não sejam comprometidas.
A integração de tecnologias como a Internet das Coisas (IoT) e a inteligência artificial (IA) na manutenção industrial tem avançado significativamente, permitindo que as empresas implementem um modelo de manutenção mais ágil e eficiente.
Com sensores e dispositivos conectados, é possível coletar dados em tempo real sobre o desempenho da máquina, facilitando a identificação de problemas antes que se tornem críticos.
Portanto, uma abordagem proativa e planejada para a manutenção assegura a performance industrial e traz benefícios adicionais, como a segurança dos colaboradores.
As falhas mecânicas podem resultar em acidentes de trabalho, e um programa robusto de manutenção ajuda a mitigar esses riscos.
A promoção de um ambiente de trabalho seguro também é um fator motivador que pode elevar a moral dos funcionários e aumentar a produtividade.
Espero que o conteúdo sobre Manutenção Industrial: A Chave para a Eficiência tenha sido de grande valia, separamos para você outros tão bom quanto na categoria Blog
Conteúdo exclusivo